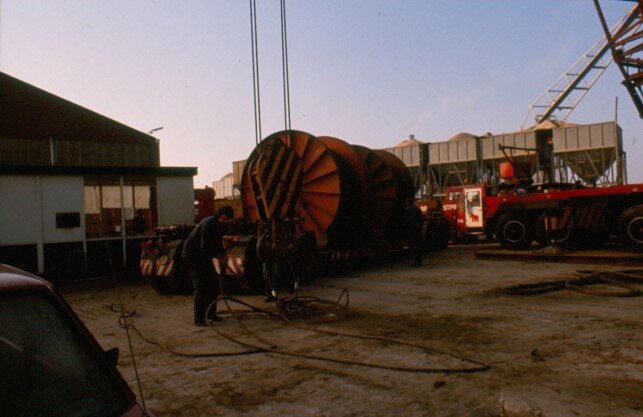
Uit de oude doos; Stormvloedkering in de Oosterschelde
Bron en auteur: Henk de Goey, oud-medewerker Mennens
In het begin van de jaren 80 is men begonnen met de afsluiting van de Oosterschelde. Wat een gigantisch project zou worden en ook vele miljarden guldens gekost heeft. Als fabrikant van staalkabels en leverancier hebben wij als Den Haan staalkabelfabriek (nu Mennens vestiging in Dongen) een aardig steentje bijgedragen aan alle werkzaamheden die te maken hadden met het natte gedeelte in dit project.
De eerste opdracht die wij van het consortium Dosbouw mochten ontvangen, was het leveren van Fenderkabels. Tussen het werkeiland Neeltje Jans en de vaste wal ontstond een stroomgat waar over een werkbrug geplaatst werd. Zo kon al het werkverkeer naar het eiland. Er waren drie sluitgaten met de namen de Roompot, de Schaar en de Hammen waar dus in een later stadium de pijlers geplaatst zouden worden.
Werkschepen
Voor alle werkzaamheden die in de Oosterschelde uitgevoerd moesten worden, waren werkschepen nodig. Bekende namen voor mensen die er nog iets van afweten zijn de Mytilus, Macoma, Cardium, Ostrea en de Johan V en op die naam kom ik nog terug. Deze werkschepen zijn in Nederland gebouwd en hebben de nodige guldens gekost, en nadat de Oosterscheldewerken gereed waren ook niet meer gebruikt zijn.
Toen kwamen ze ook op het idee, wat als deze schepen van hun werkankers zouden losslaan tijdens heel slecht weer. Zo bedachten ze een plan, we moeten voor die sluitgaten een staaldraad spannen die net op de waterlijn drijft. De oplossing was dan ook dat er om de twee meter een drijver op bevestigd moest worden, en dat het monteren van die drijvers gebeurde op de Johan V. Dan heb je daar een staalkabel in het water liggen, maar hoe kan die een schip tegenhouden wat losgeslagen is.
Aan al die werkschepen kwamen een soort haken te zitten die, als het schip was losgeslagen, zich vast kon grijpen aan die Fenderkabel. Die staalkabel was 98 mm en had natuurlijk een bepaalde lengte en gewicht en aan beide uiteinden moest daar ook nog een socket aangegoten zitten. De machine die deze kabel kon fabriceren stond op de locatie waar nu de afwikkelbok voor zware kabels geplaatst is om superslice te maken.
De kabel was tevens de zwaarste en dikste die Den Haan Staalkabel ooit gemaakt had. De socket die aan die eerste Fenderkabel was gegoten in Dongen, was aangegoten met een legering van lood en antimonium, zoals we dat toen toepasten (zie foto).
Omslachtig werk omdat alles op een bepaalde temperatuur gebracht moest worden met gasbranders. In Gorinchem hadden wij daar speciale ovens voor die zowel de gietlegering en het tin altijd op de juiste temperatuur hielden door thermostaten.
Aangieten van sockets
In de periode dat wij dat in Dongen gereed maakte, mochten we nog geen WireLock gebruiken van Rijkswaterstaat om aan te gieten. Het was toen nog niet zo gebruikelijk om WireLock als aangietproduct te gebruiken. Rijkswaterstaat vond toen dat er nog te weinig ervaring mee was om dit voor zo’n belangrijk werk uit te proberen. Toen wij de drie sockets bovenop de haspels aangegoten hadden, moest dat op transport naar Zeeland om daar aan boord van de Johan V te plaatsen.
Aan boord van het werkschip moesten wij dus, nadat een kabel was voorzien van die drijvers en de lengte was bepaald, de tweede socket aangieten. Ter plaatse aangieten was in die tijd best omslachtig vooral als het een staaldraad is van die dikte. Wat je op onderstaande foto’s kan zien aan gereedschap is nog lang niet alles.
Nadat het uitvaren en drijvers plaatsen plus het aangieten achter de rug was, wat bij elkaar twee weken heeft geduurd, kon het gereedschap naar Gorinchem.
De juiste kabellengte is essentieel
Het plaatsen van de kabels in de sluitgaten werd door Dosbouw gedaan. Daarbij bleek dat de lengte door de aannemerscombinatie niet de juiste lengte had, de eerste kabel was achteraf twee meter te lang ingemeten. Goede raad is duur, ook in dit geval waarbij alles op zeer korte termijn geregeld moest worden. Wij werden verzocht de kabel in te korten en de socket overnieuw aan te gieten. Maar dat was niet zo snel te regelen omdat, zoals je kon lezen, wij nog al het een en ander weer aan boord moesten brengen.
We hebben ze voorgelegd om de gieting dan met WireLock te doen, voor ons zou dat een stuk gemak betekenen. Plus dat we op deze manier het WireLock konden presenteren bij Rijkswaterstaat. Het werd toegestaan door Rijkswaterstaat als we het allemaal maar op zeer korte termijn konden realiseren. De andere dag stonden wij er al met ontvettingsmiddel, bankschroef, handgereedschap en 12 liter WireLock, want dat was de juiste hoeveelheid om de socket vol te krijgen. Dit was voor ons dus de eerste keer dat we zo’n hoeveelheid in één socket gingen gieten.
In de werkplaats in Gorinchem hadden we wel sockets aangegoten tot ongeveer 60 mm, maar dit was even iets anders. Kabel op lengte gemaakt en socket op de kabel geschoven, pluim gemaakt, ontvet en de socket op de juiste lengte getrokken. Met een kraan hebben we de socket en kabel opgehesen tot een hoogte dat wij hem konden bewerken. Aan de onderkant heel goed afgedicht, dachten wij.
Klaar om te gieten
Het was wel een mooie dag met volop zon en 30 graden. De poeder en vloeistof in een grote emmer gemengd en in de socket gegoten. Kijken aan de onderkant van de socket of dat het niet zou lekken, niets te zien op dat moment ging het allemaal goed. Maar even later kwam er toch wel wat door de stopverf. Het was niet meer te stoppen wat we ook probeerden, ongeveer 12 liter WireLock liep er uit.
Deze hoeveelheid was echt teveel om het in één keer te gieten. Maar wisten wij daar iets van? Gebeld om te vragen voor een nieuwe hoeveelheid WireLock, maar hoe komt dat in Burgh Haamstede vroeg mijn toenmalige bedrijfsleider zich af. Dat was snel geregeld, hij zou met zijn auto van Gorinchem naar Alblasserdam rijden en ik moest dan van Burgh Haamstede daar naar toe rijden.
Hij dacht dat het zo aardig verdeeld was met het aantal kilometers, inzicht in het aantal kilometers was hem vreemd. Maar ja wij waren al lang blij dat we dat werk nog diezelfde dag konden afmaken. Die tweede keer dat we gingen gieten was er natuurlijk niets aan de hand, want er was van de eerste keer genoeg WireLock onderin de socket blijven zitten om het goed af te dichten.
Eind goed al goed
Rijkswaterstaat had er toch wel vertrouwen in gekregen want vanaf dat moment hebben we voor het gehele Oosterschelde project onbeperkt voor allerlei doeleinden WireLock gebruikt. Al die jaren dat wij daar op al die werkschepen in het Oosterschelde project gietingen aan ankerdraden en andere werkzaamheden hebben verricht met WireLock, hebben we geen centje pijn meer gehad. Dat is heel goed uitgepakt. Dit was dus mijn eerste ervaring om met een grote hoeveelheid WireLock een gieting te verrichten.