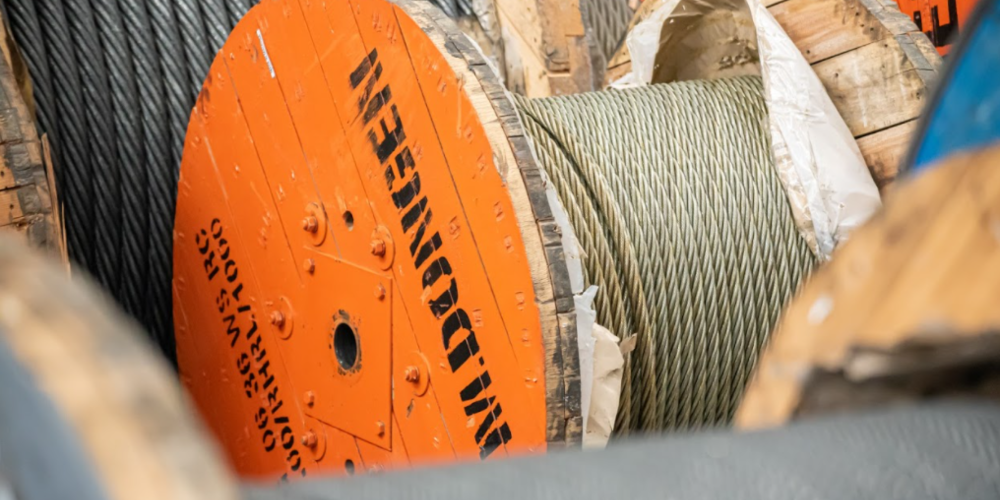
Each bend halves the service life of a steel wire rope
In many installations, the steel wire rope moves from the drum through the sheave (or sheaves) to the “dead” part (the end connection). This allows you to reroute the cable or create a delay so you can lift more weight with the same pulling force. Although no lifetime guarantee can be given on steel wire cables, Herr Prof (a.D.) Dr.-Ing. Klaus Feyrer has developed a formula to approximate the theoretical lifetime of a steel cable. The bottom line is: as a result of bending, the service life of a steel wire rope is halved. So apply sheaves appropriately, because each sheave means bending the steel wire rope – and therefore halving its life span.
The trick is to minimize the number of bends as much as possible. As a result of bending, the material fatigues and fatigue fractures will eventually occur. Are you bending a steel wire rope over sheaves? Then it is important you do this in the same direction as much as possible. Bending the rope in the opposite direction has a very detrimental effect on the life span of a steel wire rope, especially if the sheaves are placed closely together.
Important: D/d ratio
Please note that the diameter of the steel wire rope and sheave (the D/d ratio) play an important role here: a certain rope diameter requires a certain sheave. The D/d ratio depends on the cable construction, diameter, application, and use, which is laid down in the standards.
Distance between sheaves
Another point of interest is the distance between sheaves. In practice, I often see that sheaves are placed too close together. The result: accelerated fatigue of the steel wire ropes.
When bending the rope around a drum or sheave, compressive stress occurs in the single wires of the rope. This occurs right before reaching and immediately after leaving the sheave. The stress must find its way. The single wires are searching for their position, so to speak. It is therefore recommended that a minimum distance of 40 times the rope diameter be maintained between two sheaves.
Life span
The drum and sheaves affect the life span of a steel wire rope. The following points also play a role:
- the drum or sheave diameter
- the groove diameter of the drum or sheave
- the material and the toughness of the drum or sheave
- the bearing
If the sheave is too tight, the steel wire rope doesn’t have enough room to move and support in the groove. The result: a shortened service life. A groove that is too wide is also undesirable, because then the steel wire rope has too little surface to support it. This increases the surface pressure.
Wear through use
Use eventually wears down both the steel wire rope and the groove of the sheave. Over time, the wire rope becomes thinner and wears into the groove, resulting in the sheave groove becoming narrower. The new steel wire rope is mounted in a worn-out sheave, which means the support of the new rope is not optimal. The result is a shortened service life of the new steel wire rope. When replacing a wire rope, it is advised to always check whether the radius of the groove meets the standard. The hardness of the sheave groove is also a determining factor. This must match the hardness of the steel wire rope.
Contact us for an inventory
Of course, there are many other points to consider when it comes to the application of sheaves. Consider the deflection angle and material types (plastic and steel). The use of equatorial sheaves also has very specific risks. Are you wondering which sheave fits your situation? Or do you want to know if the current sheaves in your installation are used properly? We would be happy to visit you for a non-binding inventory. Please contact us.